Home › Industries › Manufacturing
Smart Manufacturing and Industrial IoT Automation
Optimise your manufacturing business, plant or factory through Industrial IoT with Hark’s manufacturing cloud system (an Intel® IoT Market Ready Solution).
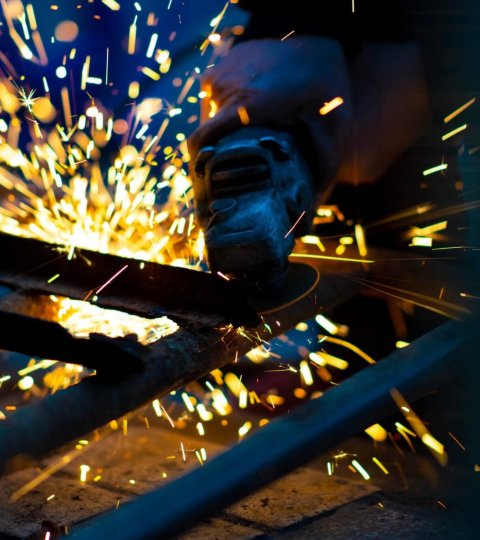
Manufacturers are constantly faced with both the burden of maximum production efficiency and the exposure of the sustainability microscope.
Facilities, devices and assets generate massive amounts of data that could be used to unlock new ways of working. Historically connectivity and visibility have been time-consuming and expensive to deploy. Hark’s IIoT solutions provide easier, new and improved ways to monitor, analyse and optimise operations.
Would you like to find out more about the Hark Platform?
Smart manufacturing with industrial IoT.
We work closely with clients to review and implement real-time remote monitoring solutions that tackle the unique needs of their facilities. The Hark Platform is agile and has been built with interoperability in mind, meaning we’re able to communicate with every asset on your factory floor.
Support for PLCs and Process Automation systems from Schneider Electric, Siemens, Allen Bradley and many, many others.
Easily collect, manage, and maximise the value from every piece of sensor data on all equipment throughout your estate.
Reduce costs and downtime by optimising assets and energy use. This reduces all operational costs and can create a new source of revenue.
Maximise the value of your data.
You will already have assets and systems in place across your plant. The Hark Platform allows you to gain remote access to that data in real-time in one easy to use dashboard.
Whether you’re measuring process values and status information, energy usage, pressure, humidity, flow, or any other metric, our installation team will work with you to bring this information to the platform with zero downtime or disruption to operations.
Rapid retrieval of data and insights such as historical readings at the click of a button.
All data immutable and safely stored in the cloud or on premise.
Easy installation and non-disruptive set up.
Use comparisons to understand patterns and anomalies in production.
Legacy Integration – not a thing of the past.
The challenge most manufacturers face is in the gathering of data. This is typical to the nature of a factory’s ecosystem, as over the years new hardware and software has been woven into the fabric of manufacturing.
This problem has been solved with the Hark Platform which has been built with the ability to connect and communicate with different devices, of different ages, that speak a multitude of different languages or protocols.
- Asset and protocol agnosticism allows a central point of view for all asset data.
- Get more out of your legacy assets and reduce maintenance costs.
- Seek out maximum optimisation by introducing alerts, triggers and automation into your plant.
- Enable remote asset performance monitoring, predictive maintenance, energy consumption monitoring and much more.
Making sensor data work harder gives you
the power of predictive maintenance.
Machine learning is a huge benefit of implementing a smart system. Not only are you able to view your sensor data in real-time, the Hark Platform starts to spot trends and anomalies in readings from day one. Providing in-depth health indication and automated proactive insight and alerting.
This allows for your maintenance schedule to be completely automated as data driven insights highlight what asset needs to be maintained and when, subsequently streamlining your supply chain requirements and making production interruptions a thing of the past.
Case Study:Revolutionising Retail
Further Reading
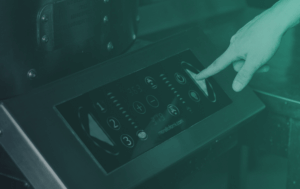
ISO 50001 Launchpad: The First Step to Your Energy Management System (EnMS)
Breaking down ISO 50001 certification into steps makes the entire process feel more manageable. By taking one important first step, you’ll have more clarity for the rest of the project…
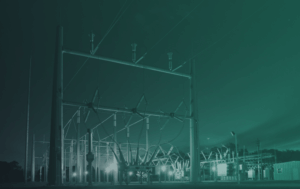
Using Energy Management Software to Minimise Energy Costs
High energy cost periods in the day can have an enormous impact on how much a business pays for their energy. Using energy management software, businesses can minimise their consumption during these hours and save money.
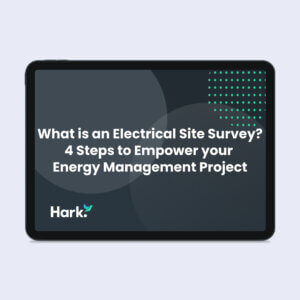
What is an Electrical Site Survey? 4 Steps to Empower your Energy Management Project
Electrical site surveys are instrumental to a successful energy management project. By understanding the assets, network infrastructure and requirements of a facility, we can accurately plan and roadmap a high-impact energy analytics and industrial IoT project.