Considering it’s estimated to be responsible for a whopping 20% of the UK’s greenhouse gas emissions (GHG), the pressure is on for manufacturers to not only talk the talk but walk the walk when it comes to implementing sustainability strategies.
The Crown Joules
90% of manufacturers are aware of the UK’s commitment to achieving its net-zero target by 2050. Many have already put processes and systems in place to tackle emissions; not only do they positively impact the environment, but they also have meaningful effects on business. Research conducted prior to the pandemic by E.ON reported that 40% of manufacturers who made sustainable measures an integral cog in their processes had increased profit margins within just 12 months.
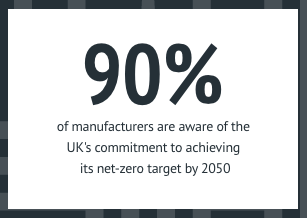
Two out of five manufacturers have invested in technical measures that aid sustainability; some manufacturers go further and generate their own energy on-site, like the Scottish Leather Group (SLC). They turn waste into heat via their Thermal Energy Plant and have recently partnered with Mulberry to recover end-of-life leather into fuel, a process that confirms their status as the lowest carbon leather manufacturer in the world. SLC’s 20 years of forward-thinking sustainability initiatives has put them well on their way to being carbon-neutral by 2025. That’s in less than 5 years.
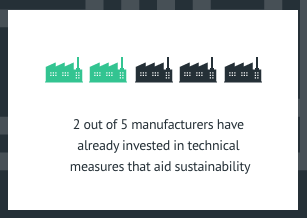
Taking action that helps reduce emissions opens the door to a range of beneficial biproducts at the same time. It’s no secret that price is one of the main drivers when choosing energy; the Government’s proposed Clean Heat Grant (2022) will provide upfront capital funding for businesses that integrate green heating technologies, like heat pumps and biomass, at their sites. What’s more, Corporate Power Purchase Agreements (CPPAs) have recently become accessible, and it’s time to take advantage. CPPAs allow manufacturers to purchase renewable electricity or green energy directly from the source, granting flexibility to fix prices paid over a time-period, usually long-term, aiding manufacturers’ planning and forecasting of wider business decisions.
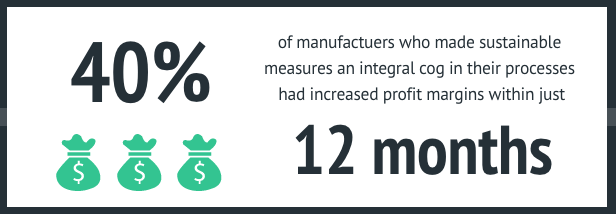
A Problem Shared is a Problem Halved
As Industry 4.0 closes in, digitalising processes has never been more important. Economics and sustainability are becoming more closely aligned to help manufacturers reach full performance potential and see benefit to their bottom line. Opportunities for improvement lie in investments in innovative equipment, improving energy effectiveness, and shortening manufacturing processes.
Improved technologies like data analytics tools and the Internet of Things (IoT) accurately analyse each phase of production, pinpointing improvement areas and opportunities to optimises processes. Applying sensors to assets on conveyor belts can automatically control when they operate, saving energy and enhancing a manufacturer’s green credentials. In addition, the latest advancements in robotics reduce human error and improve accuracy of production; speed of production is increased, and waste is reduced.
Going Around in Circles
We’re moving away from fragmented supply chains (that consequently waste energy and materials) to those in line with the 5G Factory of the Future proposal. When robotics, VR, AR, AI and the wider IoT are integrated as one, operational functionalities and logistics are streamlined, establishing the most efficient assembly lines. Full connectivity between workers, machinery, supply chain, and product allow for operational models that can be implemented for long-term sustainable and commercial benefits.
The Secret of Getting Ahead is Getting Started
The end goal is to create a circular economy where the entire product lifecycle is managed. Some low-hanging fruits include:
- Switching from artificial to LED lighting.
- Monitoring or replacing outdated assets that may be doing more harm than good.
- Making proactive assessments regarding source and lifecycle before purchase.
- Using high-quality recycled or reused materials.
Back to our friends at the Scottish Leather Company – they have adopted circular manufacturing, a regenerative model where a closed-loop system minimises the use of depleting resources and the creation of waste and pollution. The SLC already divert 80% of waste from landfill, aiming for a 100% closed-loop process into 4 years.
The manufacturing sector is embracing the ambition of the green agenda; over half of its businesses have a carbon-reducing sustainability plan. Many manufacturers are already achieving improved levels of profitability and competitiveness resultant of active decisions to minimise GHG emissions and develop sustainable manufacturing processes. It’s full green ahead on the #RaceToZero.
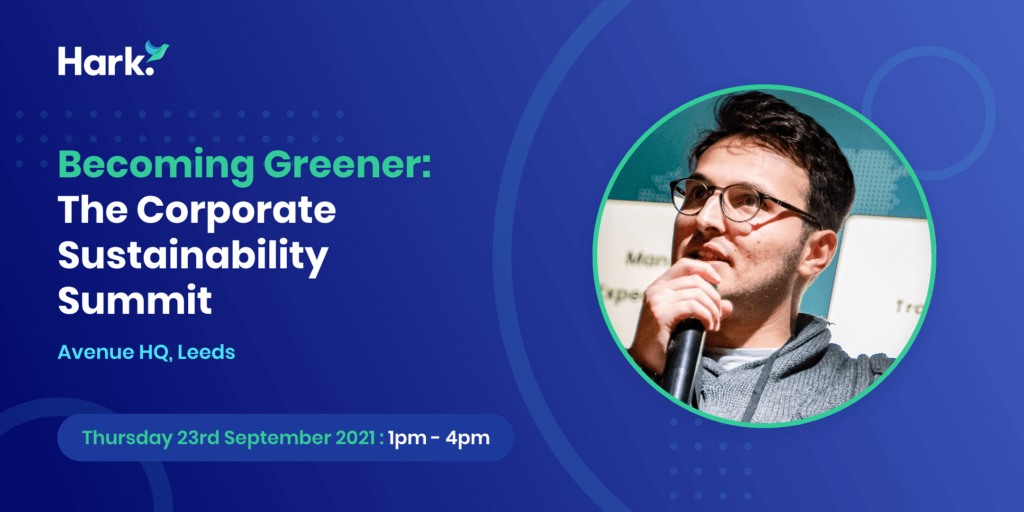
Join us at our event, Becoming Greener: The Corporate Sustainability Summit, which is taking place at the Leeds Digital Festival on the 23rd of September 2021. Our sustainable guest speakers will arm you with a brand-spanking-new arsenal of sustainable behaviour to bring to your business. From the power of data to the new age of green tech, our speakers will deliver talks on the most cutting edge sustainable business activity to help you become greener.
Thinking of going full green ahead? Join us in September to learn how to get started!